Structural Integrity
Investmech specialises in structural integrity and was involved in a quite a number of projects over the past years. At Investmech, we ensure structural integrity of machinery and structures applying experience, standards and mission profile driven requirements. In most cases analysed structure performance is confirmed by static and variable amplitude testing. Transient and quasi-static finite element analyses are done, and where required, transient dynamic finite element analysis.
We offer the following with regards to structural integrity:
- Limit state design
- Fatigue life expectancy
- Fracture mechanics
- Fracture control programmes
- Mission profile driven design and re-design
- Design for construction
- Certification
- Audit
- Welding procedure specifications
- Procedures & Specifications
Previous Work
Vibrating structures and structural integrity
Investmech’s Managing Director was part of a team that developed a unique method to reconstruct field measured responses in a test laboratory or on a dynamic simulation of the test specimen, using a state-of-the-art application of NARX models and forward-inverse-reverse-inverse system identification techniques. This technique is used extensively to define new boundaries in the field of Structural Integrity in the world. The technique allows Investmech to accurately describe how a client’s product will perform subject to a given or prescribed mission profile. A typical example of how the technique is used is where the input forces of the sea are reconstructed on a ship. This enables Investmech to prescribe new design specifications for the ship because structural inputs are known. The same technology is applied on motor vehicles and automotive components, trucks, structures, heavy equipment, buildings, etc.
Vibrating structures all over the world may suffer premature failures due to the dynamic loading caused by variable input loads. Further, with increasing pressure on production, many structures are loaded more than was anticipated in the design phase.
Investmech consultants investigate the vibration response of the structure and, based on an analysis, redesign the structure or use vibration control techniques to reduce the strain response of the structure to acceptable and safe levels. Strain response is the important objective of this process as the damage on the structure is related to the strain response and the applicable material’s fatigue characteristics.
The techniques that we use include the following:
- Vibration measurement and analysis is done by performing operating and natural mode shape, natural frequency, and maximum allowable vibration level analysis on measured signals. Frequency Response Functions, for example, are used to design isolation between screens and supporting structures. FRF’s also characterizes the responses between two channels.
- Strain gauges are applied, and strain responses measured to calculate damage at the measurement points and to infer damage at other critical points on the structure. The strain responses are also used in conjunction with acceleration responses to quantify the input forces on a test-rig or for a Finite Element Model that will yield the same time domain responses as was measured.
- Structural analysis and redesign are done using structural packages that predict the natural modes and internal loads. Redesign is then done on the package to ensure structural integrity, and manufacturing drawings are delivered.
- Structural modifications are then proposed and Investmech offers project management to upgrade the structure on site.
- Continuous condition monitoring of structures ensures that structural deterioration is detected at an early stage and condition–based maintenance scheduled accordingly.
Vehicle structural integrity
Vehicle structural integrity is ensured through mission profile driven finite element analysis and product testing. Acceleration and strain responses are reconstructed in the finite element analysis and durability testing.
Transient strain and acceleration responses of a headgear
Investmech measured strain and acceleration responses of a headgear during various mission profile driven operating conditions (trips, emergency stops, normal operation, etc.). These responses were used to predict axial, shear and bending moments on members and connections. From these, compliance with strength and fatigue requirements were confirmed. Results showed that on the structure below, thermal strains dominated the daily response.
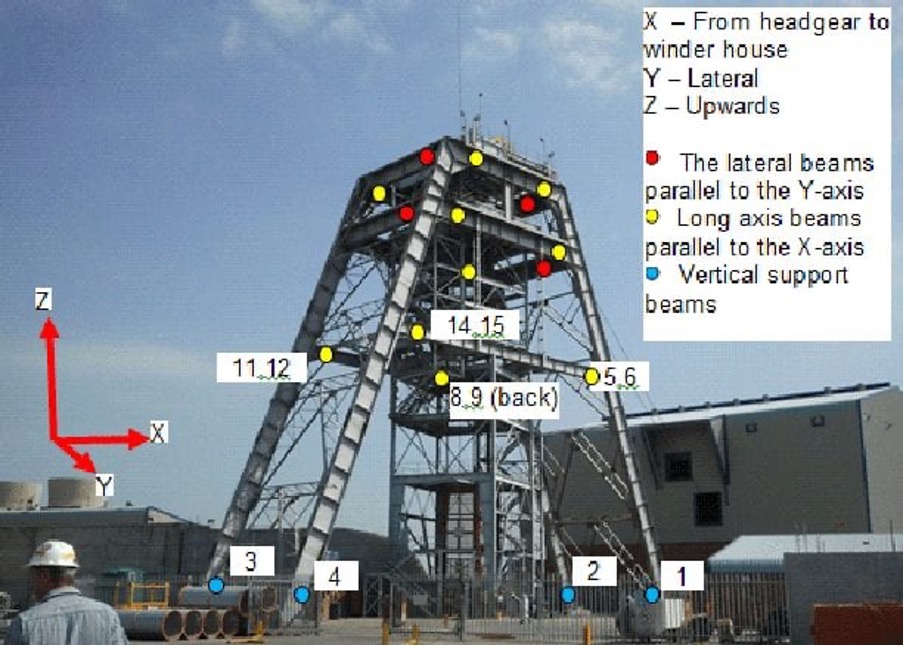
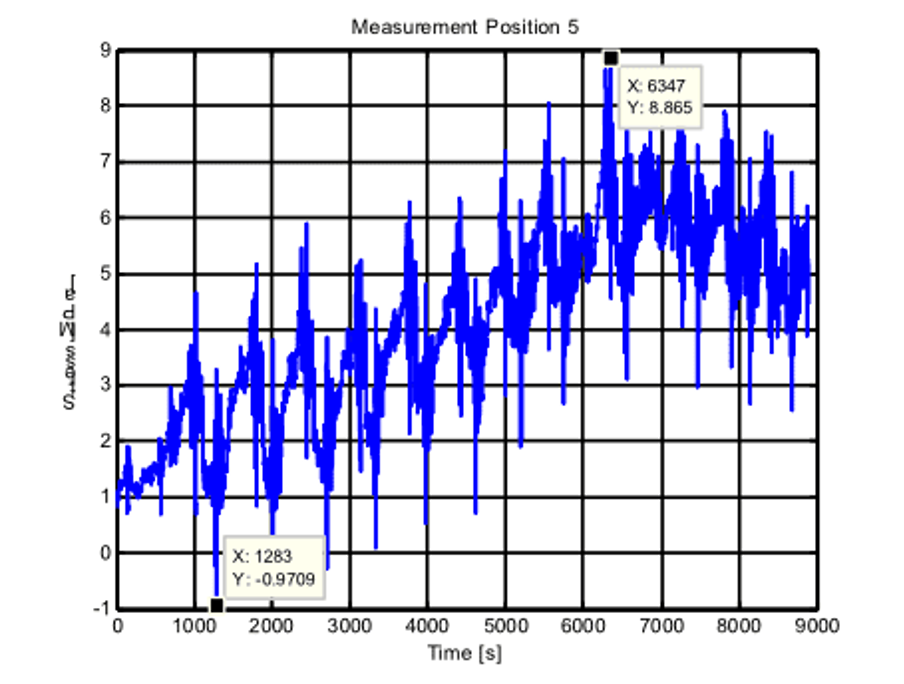
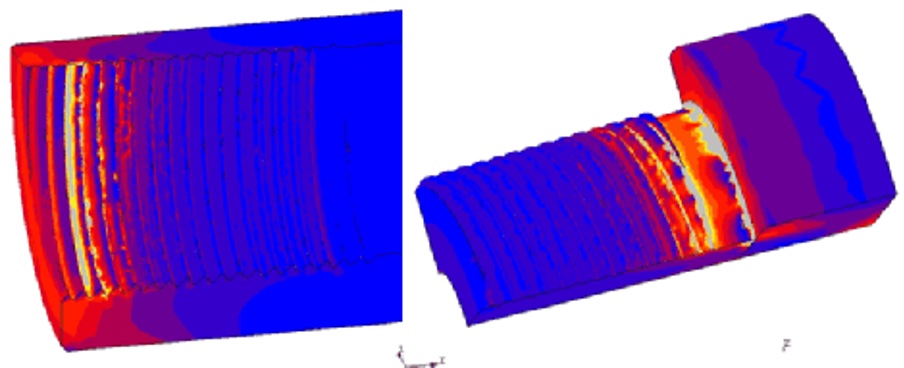
Plant and building super structures
Plant and roof super structures are analysed using finite beam element analysis.
Structural dynamics
Investmech’s experience in structural dynamics cover the modelling and integrity assurance of super structures for ships, aeroplanes, trains, plants, incline conveyors, large material handling machines and the simulation of the transient dynamics of structures during demolition.
Shaft super structures
- Calculation of structural inputs
- Testing and certification of new bolt joints
- Inspection and structural integrity audit
- Vibration measurement and operating deflection modes
- Deflection shape dependent condition-based maintenance based on MAC
Raise bore drill string structural integrity
Measured strains were used with a non-linear time and state dependent transient multi-degree of freedom mathematical model solved by the Runge-Kutta integration algorithm to find maximum and operating torque conditions. Start-up and post-stalling responses dominate design requirements.
Operating torque limits
Applying a single- and multi-degree of freedom model for the drill string with reamer, the steady-state operating torque was calculated simulating mission profile driven structural inputs. Depth dependent make-up torque was calculated to prevent unwinding of drill strings after arrest of the reamer (exceeding the breakout torque). Trip limits were calculated to prevent exceeding specific breakout torques.
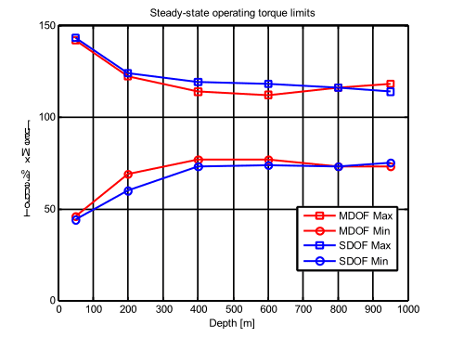
Transient analysis of structures
Investmech offers the structural integrity assessment and certification of structures subject to transient loads and consequential responses. Where the transient inputs are not known, responses can be measured on existing structures and inputs inferred using autoregressive calculations. Transient analysis of non-linear contact bodies and coupled systems are time consuming and may take a long time to complete.
System response with known transient inputs
The process:
- Generate a finite element model of the structure.
- Define the transient structural inputs and apply to the model.
- Finite element analysis based transient modelling.
- Use results for structural mechanics, vibration severity, etc
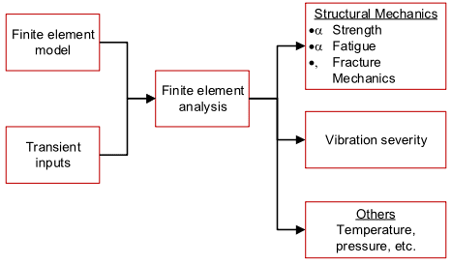
Structures under steady-state vibrating conditions
According to the lumped mass theory, the dynamic response of a super structure is the sum of the responses of the individual natural modes at their respective natural frequencies. Resonance is in most cases the cause of excessive structural responses, even a distance away from the source. Investmech ensures that vibrating sources in structures are positioned such to minimize excitation of structural natural modes (resonance). A harmonic modal analysis is sufficient for this purpose.
System response with unknown transient inputs
This is the case with existing structures giving high vibrations and unpredicted failures. The responses can be easily measured, but, the structural inputs are unknown and need to be determined for design purposes. The process:
- Responses are measured (strain, acceleration, pressure, flow, temperature, etc.)
- Mathematical model.
- Characterize the mathematical model
- ARX or NARX to iterate structural inputs
- Design modifications to ensure compliance with mission profile and standards driven requirements.
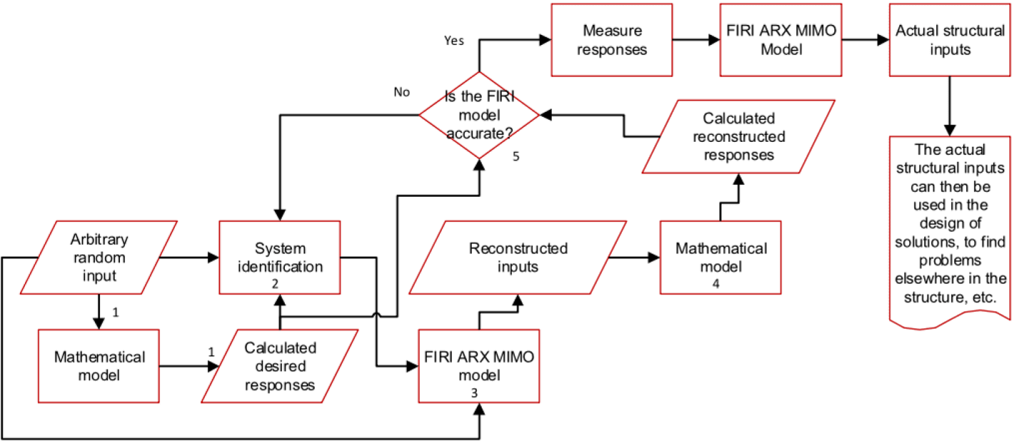
Work With Us
If you want to work with us or have any questions, please feel free to get in touch using any of the methods listed below. We will get back to you as soon as possible.
Phone Number
+27 12 664-7604
Address
8 Topaz Ave, Lyttleton Manor, Centurion, 0157
info@investmech.com