Finite Element Analysis
Finite element modelling and analysis is used as a tool in design and structural integrity assessment projects. However, it is also offered as a standalone service to our clients where the client provides us with models and structural inputs.
At Investmech, we add value to the field of Finite Element Analysis by being one of the experts in the world that reconstructs input forces for measured strain and acceleration responses. The MSC and ANSYS suite of packages are used for finite element analyses. We also use Prokon for finite beam element analysis on structures.
We also offer numerous testing services (read more) where we have specialists that can develop test standards and test specifications according to our customers’ needs and requirements. We use state-of-the art time domain reconstruction software to reconstruct structural inputs and responses in the time domain that is used for finite element analysis and testing.
We also developed ResRecon, a PC Matlab based algorithm to assist Finite Element Specialists to identify input forces for measured responses. We have unique experience in this field. (You can view our full list of software and hardware products that we developed here)
How we apply finite element analysis in problem solving and design
Typical work that are performed
- Solve resonance in structures and automotive vehicles
- Design hoisting systems and elevated platforms
- Determine temperature distributions
- Using finite element analysis as part of a virtual product development strategy allows Investmech to introduce new products into the market faster and at reduced cost. This reduces the number of prototypes needed whilst introducing a broad scope for optimisation.
- Solve engineering problems
- Design new components
- Audit designs and do modifications to ensure compliance with international standards and mission profiles
We have vast experience in transient finite element modelling and analysis:
- Crash simulations between vehicles
- Thermal and structural coupling in heat transfer calculations for furnace and ladle design
- Liquid and structural coupled modelling to design lids for liquid metal transport ladles
- Towing devices
- Vehicle dynamics & fatigue
- Heat exchangers
- Pressure vessels
- Stacker / Reclaimers
- Dragline super structures
- Piping
- Warping due to welding, especially close to bearings
- Computational fluid dynamics (CFD)
- Nuclear reactors
- ROPS & FOPS
- Ship loaders
- Material handling super structures
Previous Work
Refractory lining erosion
Investmech programmed and solved a quasi-static adaptive mesh finite element model in Matlab to simulate and understand the erosion of refractory, especially at the slag line. Model parameters were verified against measured erosions and subsequently used for the design of refractory at the slag line.
Induction furnace and refractory lining
Investmech developed a mathematical model to reconstruct the behaviour of the non-linear refractory lining in furnaces. Accuracy was verified by strain measurements. The model has been used in several analyses for the design improvement, or life extension confirmation of furnaces.
LDV load box fatigue
Resonance resulted in reduced fatigue life of a LDV load box. Investmech calculated mission profile driven road inputs to reconstruct measured strains and accelerations. A transient dynamic analysis was then carried out to confirm the fatigue life of design modifications to the load box. The product was verified by testing.
Warping due to welding
A client had to make a weld close to the slew bearing contact surface between the dragline and its tub / base. Investmech optimized the weld procedure to minimize the deflection of the bearing contact surfaces after welding.
Reconstruction of dragline boom incidents
Investmech reconstructed several boom failures as part of root-cause analyses programmes. This provided an understanding and clarity on why a specific incident occurred. In one such assessment, local buckling of a boom chord after impact with the bucket was reconstructed to determine root-cause of failure.
Optimization of lace-chord connections in dragline booms
Investmech optimized the connection between laces and chords of dragline booms by starting with a solid piece of steel the model of which was gradually updated to achieve a stress distribution below those values that result in crack initiation and collapse. Structural inputs were determined from strain reconstructions. The parts were manufactured and installed, see the installation of one of the laces below. The BS 7608 fatigue code was applied for fatigue design of the weld detail. The advantage of this process is that the final profile is calculated by Patran to result in the mission-dependent allowable stresses.
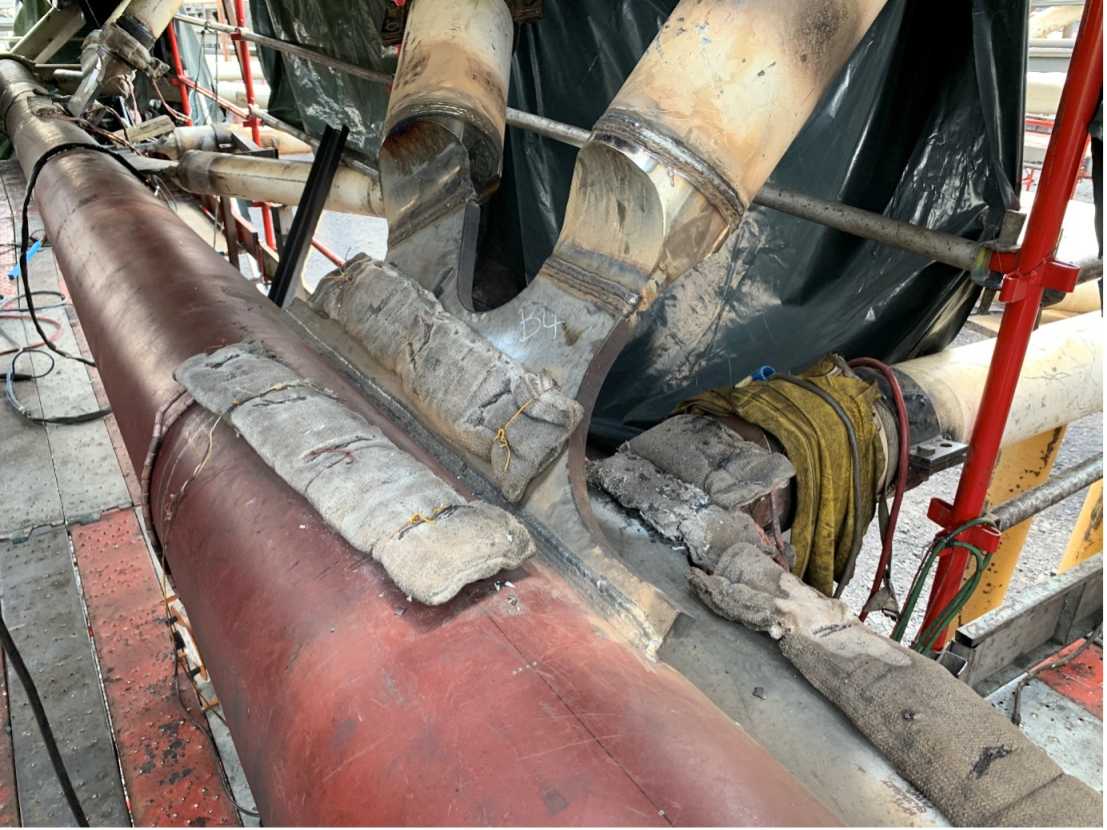
Finite element analysis of furnaces, ladles, refractory
At Investmech, we have vast experience in the accurate modelling and simulation of transient (and steady-state) furnace or ladle thermal and structural responses. Applying international accepted material compliance criteria designs are produced that complies with user requirements. State-of-the-art analysis software is pushed to the limit to model refractory bricks in contact with each other.
Finite element modelling of fluids in containers – sloshing
Slosh and sloshing of liquid aluminium during impact was calculated to find crash dependent forces on the lid of a liquid metal ladle. These forces were used to design sufficient clamps and stiffening of the lid to prevent leakage during potential accidents.
Steel casting failures
Investmech determined the root-cause for self-destruction of a kiln roller and riding ring after casting. The time and temperature dependent phase transformation distribution of the alloy in the cast was calculated ignoring transformation creep and plasticity. From the residual microstructure distribution, the residual stress was calculated, which, with the surface roughness of the cast explained the self-destruction of the cast. Investmech modified the pattern design to have a mould that will enable a more uniform phase transformation distribution and resulting microstructure distribution. The solution was applied and solved the problem.
Other projects
Ship loader integrity
Investmech quantified the integrity of new ship loaders for the South African harbors.
Ship loader collapse
Investmech determined the root cause for the collapse of two ship loaders at Saldanha Bay.
Work With Us
If you want to work with us or have any questions, please feel free to get in touch using any of the methods listed below. We will get back to you as soon as possible.
Phone Number
+27 12 664-7604
Address
8 Topaz Ave, Lyttleton Manor, Centurion, 0157
info@investmech.com